Feed processing technology - Effect of grinding particle size on feed quality
Grinding is an essential part of feed processing and an effective way to improve the digestibility of feed for livestock and poultry. Its purpose and function are to improve the utilization value of materials and improve the processing quality of feed products. Grinding process is an important procedure to improve feed quality during feed processing and is also one of the necessary means to make rational usage of feed. The size of the crushed particle should be determined according to the types of raw materials, the type of feeding animals, growth stage, and technological requirements. Too coarse or too fine particle size have disadvantages and cannot reach the best production status.
1.The main factors that affect the particle size of materials
1) Grinder types: different types have different grinding effect. The main models of grinders are:
① Hammer mill is characterized by simple structure, easy maintenance, good versatility and good adaptability, good safety and high production efficiency.

ZHENG CHANG SFSP 56×40a Hammer Mill
② Roller grinder is characterized by high productivity, low energy consumption, less dust, uniform particle size, less temperature rise after being crushed, and less water loss.
③ Claw-type grinder, the finished product is fine, can handle wet material with greater viscosity and without blocking. Its grinding process also has mixing function, is a kind of small grinder widely used in the countryside.
④The micro pulverizer and the ultra-micro pulverizer are mainly used to grind premixed materials and special aquatic feed, characterized by fine particle size.
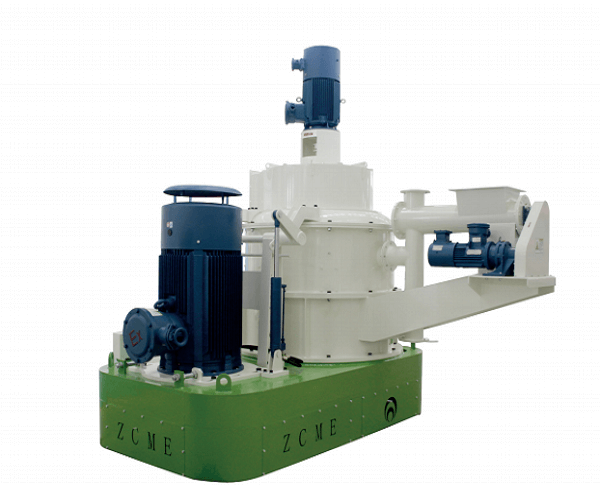
ZHENG CHANG SWFL 128D Vertical Micro Pulverizer
2) Hammer is the main wearing part of grinder. Its shape, size, working density and layout have effect on the output, electricity consumption and product quality of the grinder.
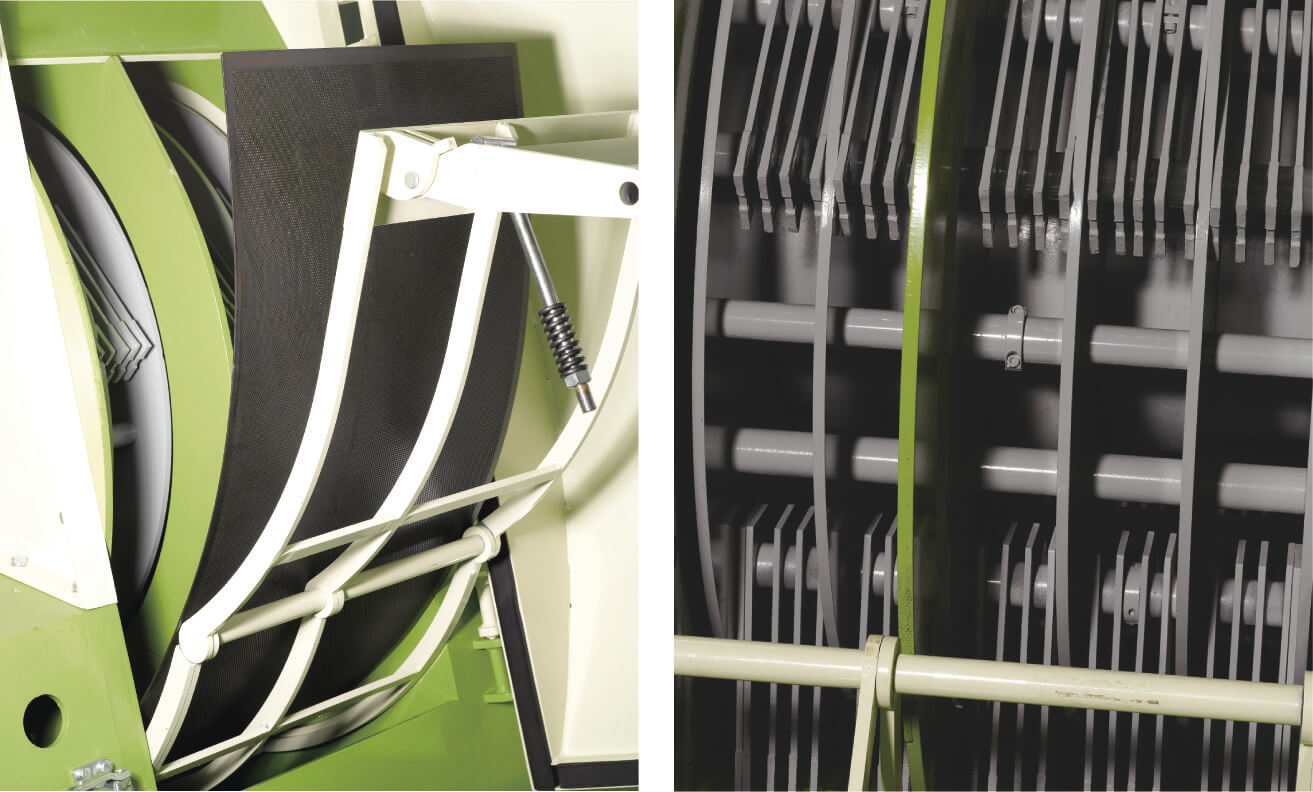
3) The tip linear velocity of hammer: in a certain range, the greater the tip linear velocity of hammer, the higher the productivity of grinder and the lower power consumption of unit product. But too faster speed will increase no-load power, vibration and noise, decrease the grinding efficiency.
4) Screen size and opening rate: the larger the sieve pore, the greater the output of crushed materials, and the coarser the material pellets; With the same sieve pore, the larger the opening rate, the greater the output of crushed material, and more uniform the material particles. But too large opening rate will reduce the strength of the screen and shorten the service life.
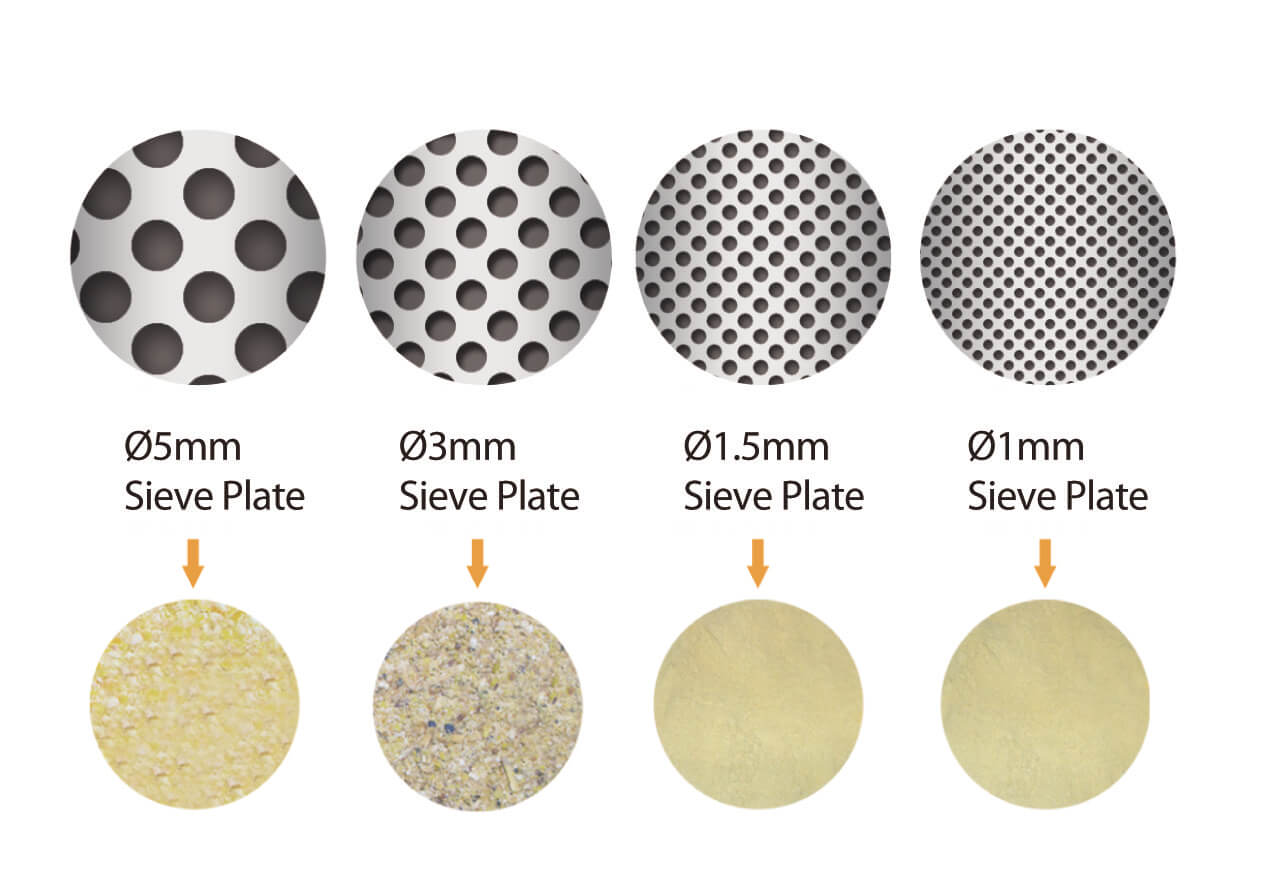
5) Sieve wrap angle: the larger the screening wrap angle, the larger the screen area and the higher the crushing efficiency.
6) Clearance between hammer and screen: The clearance is the distance between the top of hammer and the inner surface of screen when rotor is running. It is an important factor affecting the crushing efficiency. Too large or too small clearance will increase power consumption, reduce grinding efficiency, and make the particle size of crushed material uneven.
7) The structure of grinding chamber and the installation of toothed plate: all of them can effectively destroy the material circulation layer, increase the number of effective hits to the material, and thus improve the grinding efficiency.
8) Discharging way: discharging device should be able to discharge and convey the crushed materials in time. At present, there are three kinds of discharging ways: self-weight dropping, pneumatic conveying and mechanical conveying plus wind suction. Mechanical conveying plus wind suction has best effect, which is the main discharging way used by large grinder at present.
2.Effect of particle size on feed utilization
Some raw materials, such as corn, wheat, rice, soybean etc., have hard and dense skin. If they are directly used to feed livestock and poultry, the digestive juice is difficult to immerse the inside. After being crushed, the cereal skin is torn and the internal nutrients are exposed, to ensure that the material has a larger surface area, the digestive juice is easier to immerse the material, and improve the digestibility of animal feed.
Studies have shown that the digestibility of grain with diameter of 0.85 ~ 0.95mm is increased by 3% to 5% compared with diameter of 1.7 to 1.8mm. At the same time, the material after being crushed improves the palatability of livestock and poultry, and reduces the consumption of feed energy, thus reduces the utilization rate of feed.
Certainly, too fine material does not mean better effect. The size of the general particle from 0.5 to 2.0mm is suitable, which varies according to different varieties of livestock and poultry, the feeding stage and raw materials. Because too fine feed will make the palatability of livestock and poultry worse, the material will be stuck in the mouth, difficult to swallow. At the same time, too fine material easily causes stomach ulcers in livestock and poultry. Moreover, it will increase the power consumption of feed processing, reduce the output, increase the wear of grinder and its parts like hammer, screen and so on, and reduce the service life.
Studies have shown that the digestibility of grain with diameter of 0.85 ~ 0.95mm is increased by 3% to 5% compared with diameter of 1.7 to 1.8mm. At the same time, the material after being crushed improves the palatability of livestock and poultry, and reduces the consumption of feed energy, thus reduces the utilization rate of feed.
Certainly, too fine material does not mean better effect. The size of the general particle from 0.5 to 2.0mm is suitable, which varies according to different varieties of livestock and poultry, the feeding stage and raw materials. Because too fine feed will make the palatability of livestock and poultry worse, the material will be stuck in the mouth, difficult to swallow. At the same time, too fine material easily causes stomach ulcers in livestock and poultry. Moreover, it will increase the power consumption of feed processing, reduce the output, increase the wear of grinder and its parts like hammer, screen and so on, and reduce the service life.
3.Effect of particle size on the mixing uniformity of feed
The particle size of the material affects the mixing uniformity of feed. According to the test, it is found that the smaller the average particle size of mixed material is, the more uniform particle size is, the slower mixing speed is, the higher mixing uniformity can be achieved, and not easy to produce the classification phenomenon during the subsequent transportation and storage. On the contrary, when the material with different particle diameters are mixed, the uniformity of mixing can be poor. Therefore, in terms of mixing process, the crushing particle size of various raw materials is required to be smaller and similar, so as to achieve good mixing effect and ensure product quality.
4.Effect of particle size on pelleting
The particle size of materials has a great effect on the pelleting process and feed quality. The same materials with different particle diameter and size produce feed with different quality. At the same time, the fine material can reduce the wear of the die and produce feed with smooth appearance, compact structure, low powder rate and without crack. After testing, the maximum particle diameter of materials to be pelleted is not larger than half of ring die’s aperture, and the proportion of particles above 1mm is not more than 20%. Then the ideal particles can be produced and the negative effects of too fine materials can be avoided effectively.