Processing and application of extruded sinking fish feed
According to the feeding features of different aquatic animals, benthic animals like river crab, which are used to finding food at the bottom of water and using a slower way of eating, the feed pellets cannot be too hard, and minimize the loss of small debris during eating process. Therefore, the sinking extruded feed is more suitable, it is easy to absorb water and to be soften, also can reduce the loss of small debris, the feed waste and water pollution. Moreover, extruded feed has long water resistance and high maturity.
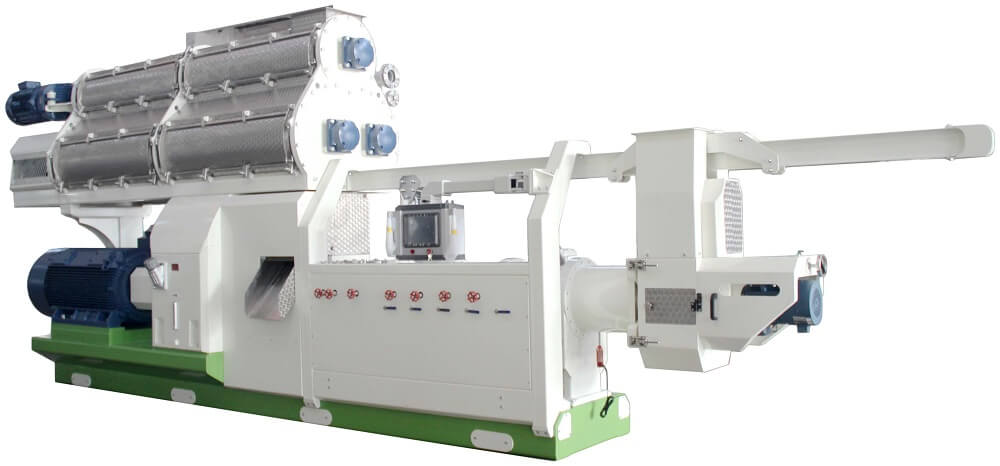
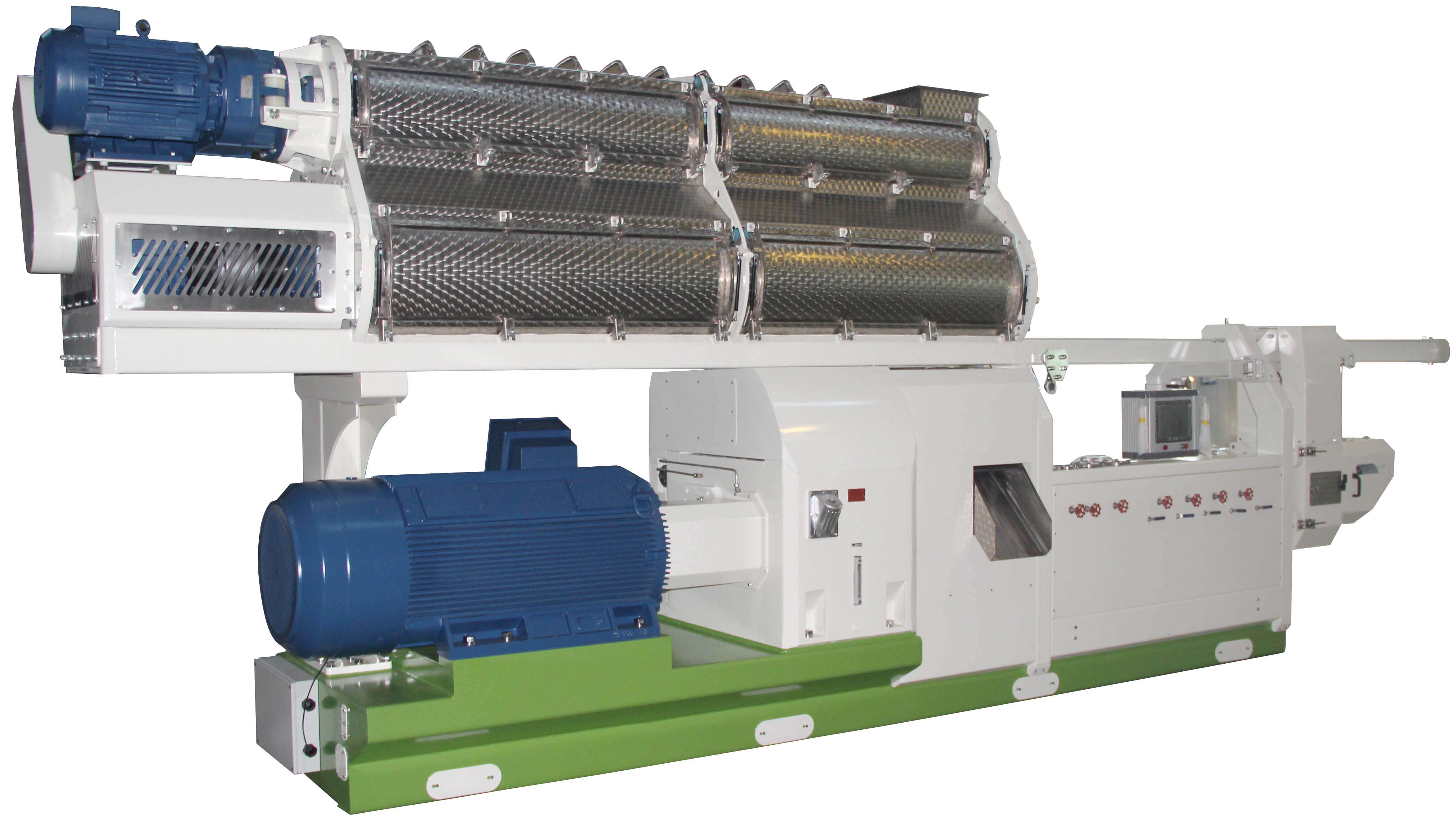
ZHENG CHANG SPHS 268F Aquatic Feed Extruder
A new type of conditioner has been equipped to make the final feed maturing degree and uniformity better than the traditional ways.
Use a kind of general-purpose equipment to produce floating feed and sinkable feed according to the demands.
The double-screw wet extruder is widely used to produce extruded feed. There are many factors that affect the expansion of materials, but they are mainly related to conditioning, extruder operation, and material characters. We can control the sinking and floating properties of extruded feed by changing the extrusion conditions.
Use a kind of general-purpose equipment to produce floating feed and sinkable feed according to the demands.
The double-screw wet extruder is widely used to produce extruded feed. There are many factors that affect the expansion of materials, but they are mainly related to conditioning, extruder operation, and material characters. We can control the sinking and floating properties of extruded feed by changing the extrusion conditions.
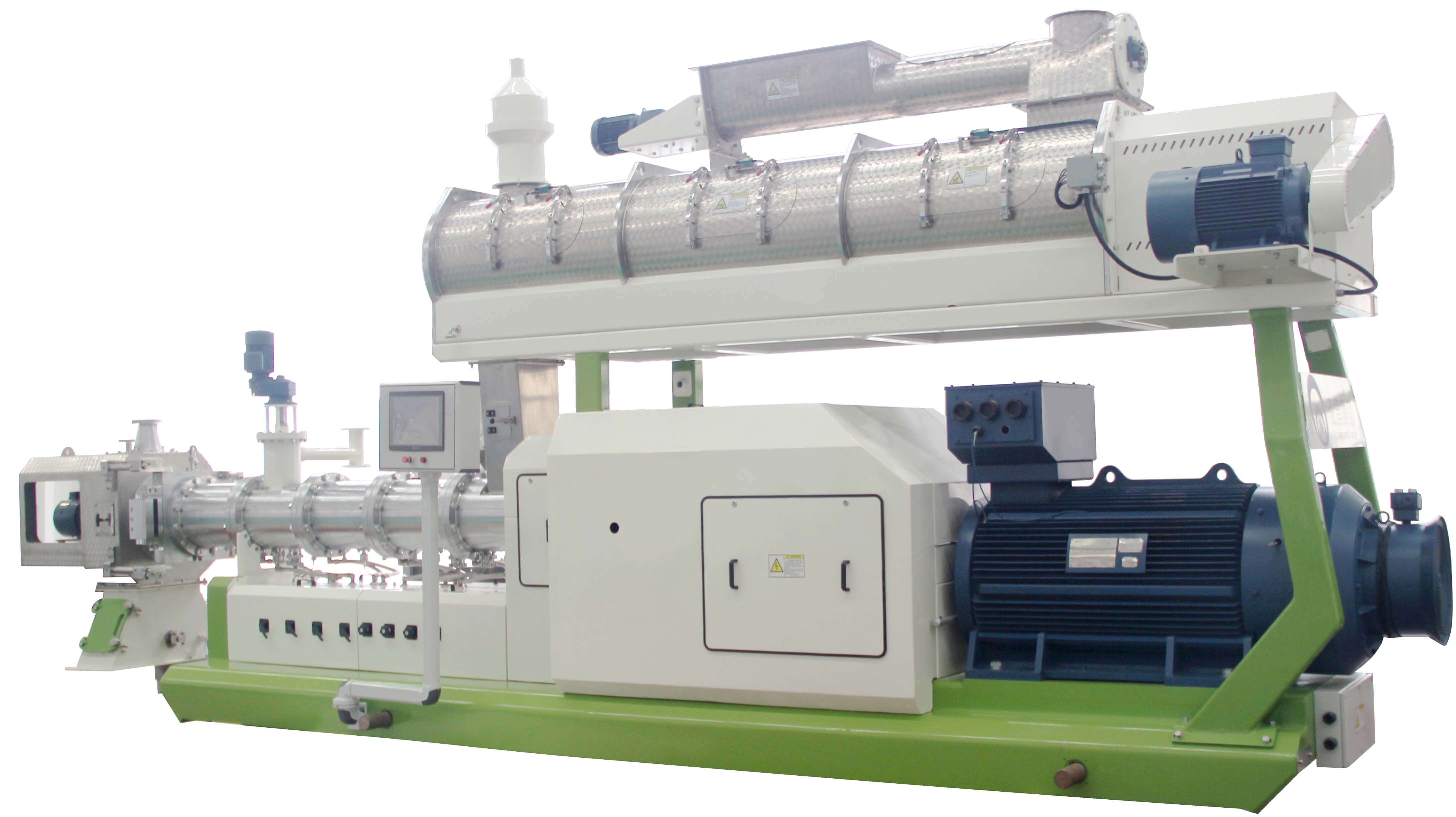
ZHENG CHANG SPHS 130×2 Double-screw Aquatic Feed Extruder
Precise and unique double-screw structure increases oil content up to 22%.
It can process fast sinking material (such as shrimp feed) with about 30% starch.
Produce 100% floating feed and 100% sinkable feed only with a kind of screw.
1.Conditioning plays a particularly important role in the production of sinking extruded feed. When producing sinking extruded feed, we should weaken the strong effect of extrusion to enhance the effect of conditioning. Adding water and steam when conditioning and enough conditioning time can soften and mature the material fully, and can create better extruding conditions. In this way, the material can be further matured and made into sinking feed without larger extrusion degree. Adequate conditioning can improve the digestibility, water resistance of feed, and improve the stability of extrusion, namely the uniformity of products.
It can process fast sinking material (such as shrimp feed) with about 30% starch.
Produce 100% floating feed and 100% sinkable feed only with a kind of screw.
1.Conditioning plays a particularly important role in the production of sinking extruded feed. When producing sinking extruded feed, we should weaken the strong effect of extrusion to enhance the effect of conditioning. Adding water and steam when conditioning and enough conditioning time can soften and mature the material fully, and can create better extruding conditions. In this way, the material can be further matured and made into sinking feed without larger extrusion degree. Adequate conditioning can improve the digestibility, water resistance of feed, and improve the stability of extrusion, namely the uniformity of products.
2.The extruded sinking feed should use lower screw speed, which can provide the required extrusion shearing effect, without producing excessive pressure, and avoid a sharp increase in material energy, otherwise, it is not easy to produce sinking feed with overlarge expansion ratio through the die hole.
3.The control of cavity temperature is another important aspect of material energy control. In the feeding section of cavity, it cannot be heated to ensure good conveying performance. In the melting section of cavity, the temperature must be maintained at 120~125℃, should not be too high. Screw and machine cavity can shear and knead material, so as to accelerate material maturation and plasticity. In the homogenization section at the end of cavity,
the temperature should be cooled at 40~50℃, to reduce the energy of the plastic material that has already been matured, reduce the oversaturation state of the moisture in the material,and avoid over-extruded material when it’s extruded into the atmosphere from the die hole.
3.The control of cavity temperature is another important aspect of material energy control. In the feeding section of cavity, it cannot be heated to ensure good conveying performance. In the melting section of cavity, the temperature must be maintained at 120~125℃, should not be too high. Screw and machine cavity can shear and knead material, so as to accelerate material maturation and plasticity. In the homogenization section at the end of cavity,
the temperature should be cooled at 40~50℃, to reduce the energy of the plastic material that has already been matured, reduce the oversaturation state of the moisture in the material,and avoid over-extruded material when it’s extruded into the atmosphere from the die hole.

4.The extrusion ratio of sinking feed is usually less than 1.3, which is different from that of floating feed which can reach 2 or more than 3. The pressure inside the machine cavity is related to the screw configuration, material properties, opening rate of die plate and feed volume of the extruder. The opening rate affects the pressure of the material inside the cavity. The larger the opening rate is, the larger the discharge volume is, and the higher pressure is not easy to accumulate at the die plate. During the trial production, the number of die holes can be changed according to the situation, to produce suitable extruded sinking feed.
Extruded sinking fish feed successfully solved the problem of the low maturity of hard pellets in traditional way. In addition, extruded sinking feed has high stability in water, no artificial adhesive, no collapsing and no dispersing, so it has been widely used in fishery and is gradually replacing hard pellet feed.
Extruded sinking fish feed successfully solved the problem of the low maturity of hard pellets in traditional way. In addition, extruded sinking feed has high stability in water, no artificial adhesive, no collapsing and no dispersing, so it has been widely used in fishery and is gradually replacing hard pellet feed.